Newsletter
- chrisbett2010
- Feb 11, 2019
- 2 min read
Chris Bettencourt Cedar City Mechanical Engineering Creativity Track
3D Printing Business
3D Printing to the average person may seem futuristic and out of reach. My goal was to change that, at least for a few people. As an Engineering major I’ve always loved manufacturing, but I didn’t have a lot of experience with it. Education can only get you so far. I wanted to experience something. I got in touch with a local business and asked if I could help improve their process and productivity using 3D printing. A problem was brought up where thermostat wires were always messy to look at and if you used tape to organize them it didn’t look good. I decided to focus on this problem and came up with a small clip that would hold the wires in place and make the job look more professional. The installers were really excited about them and they had some tips to make them more efficient. My final product came out to look like the two used below, attached using a sheet metal screw.

I was inspired to do this product from the endless possibilities I explored while learning about 3D printing. I think it’s a tool that can benefit anyone and every business. Some people are using 3D printers to make prosthetics and others use them for making retainers. With fairly little training and less than 200 dollars anyone can make a customized plastic part. If you want to go bigger, you can print using wood filament or nylon too. That’s what’s so inspiring about this process.
One challenge in creating these 3D prints was assembling the printer itself. It took a lot of investigation and research to make sure I had the machine calibrated correctly and it can be a pretty steep learning curve if you want to get into the mechanics of it all. I had some trouble with the plastic adhering to the build plate and learned how to level the plate correctly so that it was a perfect distance from the nozzle to make a clean print.
Other than the HVAC company I did the prints for, I also helped the Engineering Department at SUU to improve one of their labs. In materials science, students have to make homemade plastics and then mold them by hand into something. I decided to create a mold using the 3D printer that would give them a nice clean model to use when they make their plastics. It turned out to be the Death Star. I got the download of this model from a site called Thingiverse.
This project really helped me to realize that experiencing something is very different from just reading about it. When you see a part actually being built it takes on a new understanding. When a part fails because you designed it a certain way you learn to diagnose the problem and find a viable solution. I think this has really broadened my skills as an engineer if only in my critical thinking and 3D modeling skills.
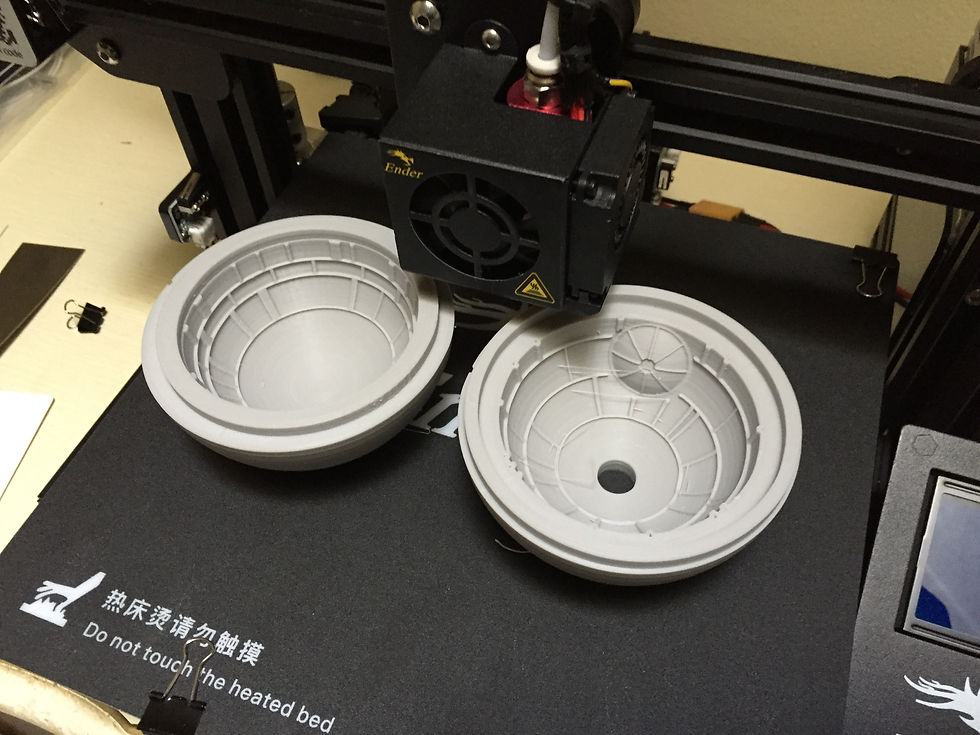
Kommentare