Bushing Embeder Machine Design
- Christopher Bettencourt
- Aug 1, 2020
- 1 min read
Updated: Jan 29, 2021
In machine design, we had to create an original machine that would help to accomplish a task. My machine was in reference to a problem I was experiencing at work. I wanted to heat up drill bushings and embed them into 3D printed drill jigs for aerospace parts. I set to work developing a holder for a soldering iron that would then move precisely using stepper motors in order to hole the necessary positional tolerances.
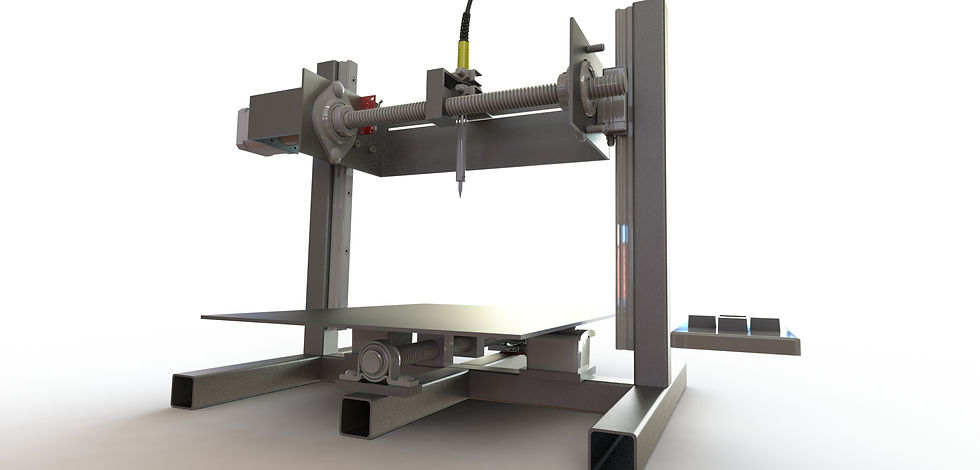
Design Steps
The first step was to determine what the customer needs were for this product. It had to be capable of holding very tight positional tolerances - approximately .001 inches. It had to be repeatable, relatively quick, and affordable to produce.
A house of quality was then used to determine what the most important features were. This is then used to give priority to the most crucial components of the design. In this case, the positional tolerance, ease of assembly, and impact resistance were the top priorities.
Next, concept generation was performed in order to find which component would be best suited to fulfill the needs.
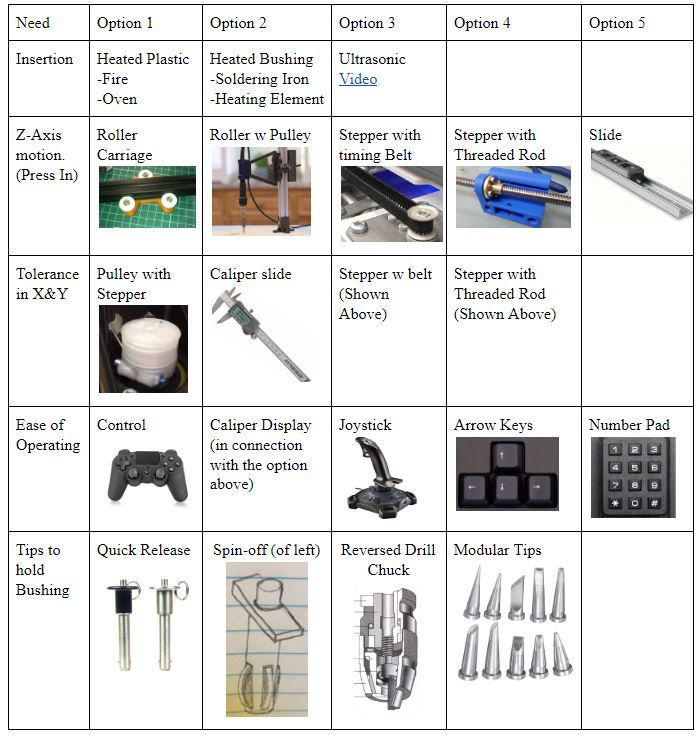
The preliminary design was created following criteria that would allow me to determine which component was best.

Final Steps
To finish the bushing embedder, I next determined the areas that would most likely fail and determined the best reinforcements for those areas. Next, I created a CAD 3D model of it with components from Mcmaster Carr and some custom pieces. To view the drawings and Bill of Materials, view the PDF report.
To view a video and animation of this machine, click this LINK.
Comments