Metal Additive Research
- Christopher Bettencourt
- Jan 11, 2022
- 3 min read
Updated: Nov 13, 2023
The U.S. Department of Energy funded this research on development of a metal 3D printed recuperator for use in concentrated solar power systems.
Recuperators are heat exchangers that help increase efficiency in power production through preheating the working fluid coming into the system with the excess heat of the exiting fluid.
Concentrated Solar Power (CSP) are systems that utilize mirrors to concentrate sunlight onto a tower that heats up the working fluid to turn a turbine that will generate electricity.
Recuperators are expensive because they use costly high-temperature alloys in their construction. To offset some of the material cost, we can substitute part of the recuperator with a low-temperature material like stainless steel. This is possible because there is a low-temperature/pressure side of a recuperator where incoming fluid is cooler and the exiting fluid is transferring energy to the incoming fluid making the exiting fluid cooler when it exits. The catch is, combining two materials (one low-temperature and one high-temperature) can be difficult to do and therefore costly.
Metal Additive Manufacturing (MAM): This is a manufacturing method which can allow for parts to be built layer by layer. Using a Directed Energy Deposition machine, different metal powders can be mixed with varying compositions to create a Functionally Graded Material (FGM). This means that there is a gradual transition between one material and another (see below).
The first step is to get some preliminary data that we can use to compare to the FGM samples. Microstructural behavior is examined as well as Tensile properties for 3 materials. Two nickel-based superalloys, Inconel 625 and Haynes 282, and one iron-based alloy, namely stainless steel 316. The stainless steel will be used as the low-temperature material considering its lower strength at high temperatures when compared to nickel superalloys.
Microstructure
Using a Scanning Electron Microscope, we can gain valuable insight into the properties of a material such as it's predicted yield strength based on grain size and morphology.
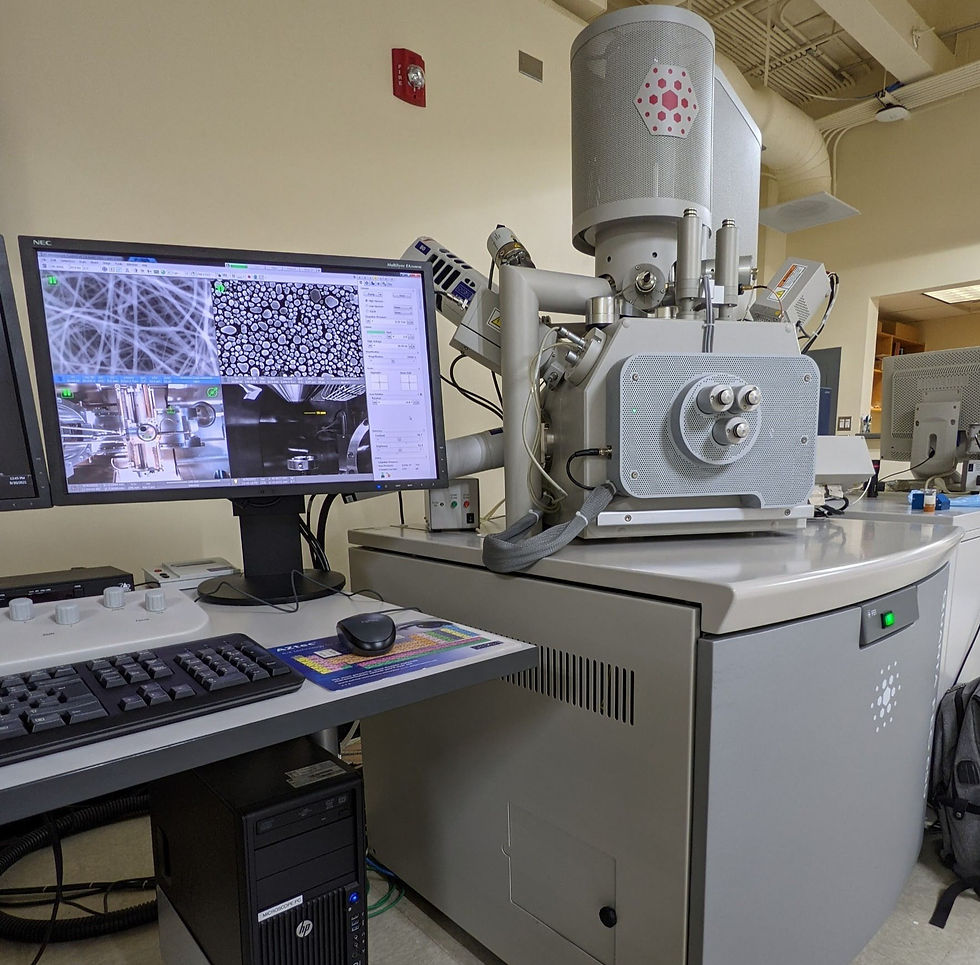
Inverse Pole Figure (IPF) maps can be created using Electron Backscatter Diffraction (EBSD) to determine the orientation of the grains as they solidified. See the samples on the left below with the IPF map on the right.
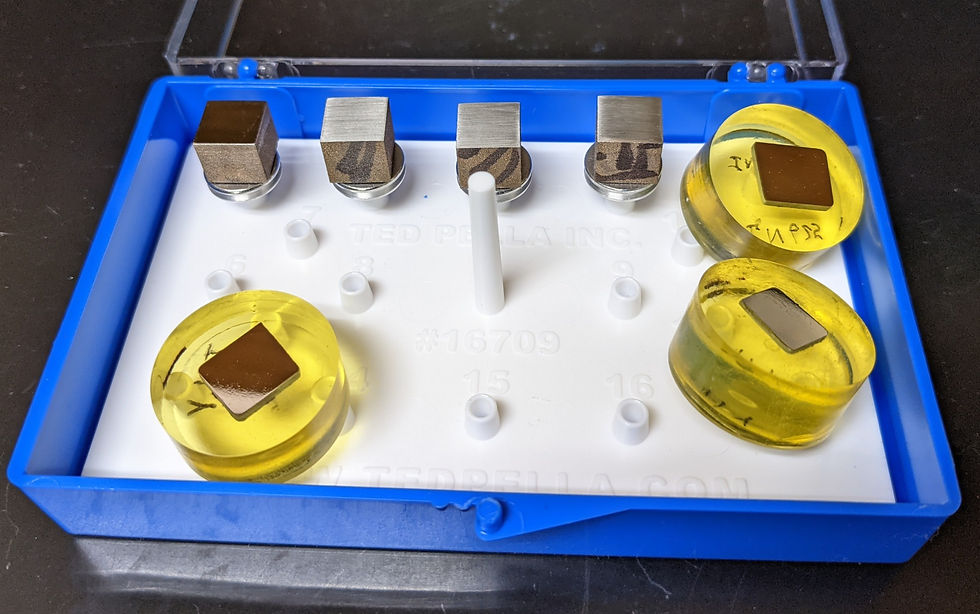

Tensile Testing
The tension testing is performed using a machine powered by servo-hydraulic motors that acquires displacement and force data to be further processed. Dog-bone shaped specimens are put into the jaws then pulled apart until fracture.
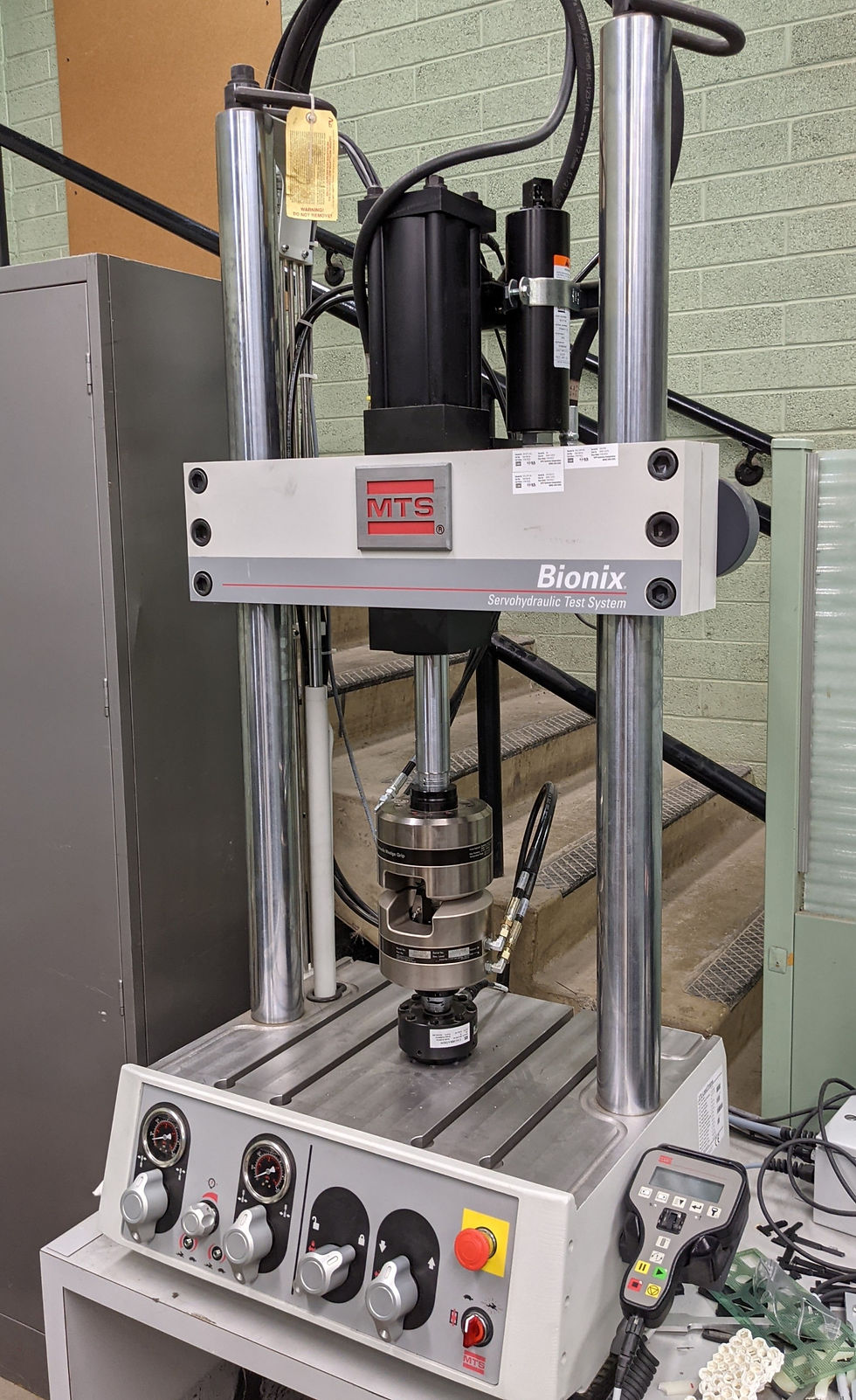
A fractured sample is shown below.

The data can be post-processed into a stress-strain curve using Matlab. The tensile results describe the behavior of the material when stress is increased as it is being stretched by the machine. Strain is measured as an elongation percentage of the original length and determines the ductility of a material. The conventional Stainless steel (SS316L) demonstrates a very ductile material with a percent elongation of nearly 80% of the original length, while additively manufactured SS had an increased yield strength. The FGM samples surprisingly resulted in an increased yield strength even compared to the single alloy counterparts built by AM.
Future Testing
In the near future, tests will begin on FGM samples and results can be compared to the preliminary results in order to predict how close the FGM material is behaving compared to its constituents.
Other concerns will be investigated, like particles that seem to reduce the part strength. These particles are shown below.
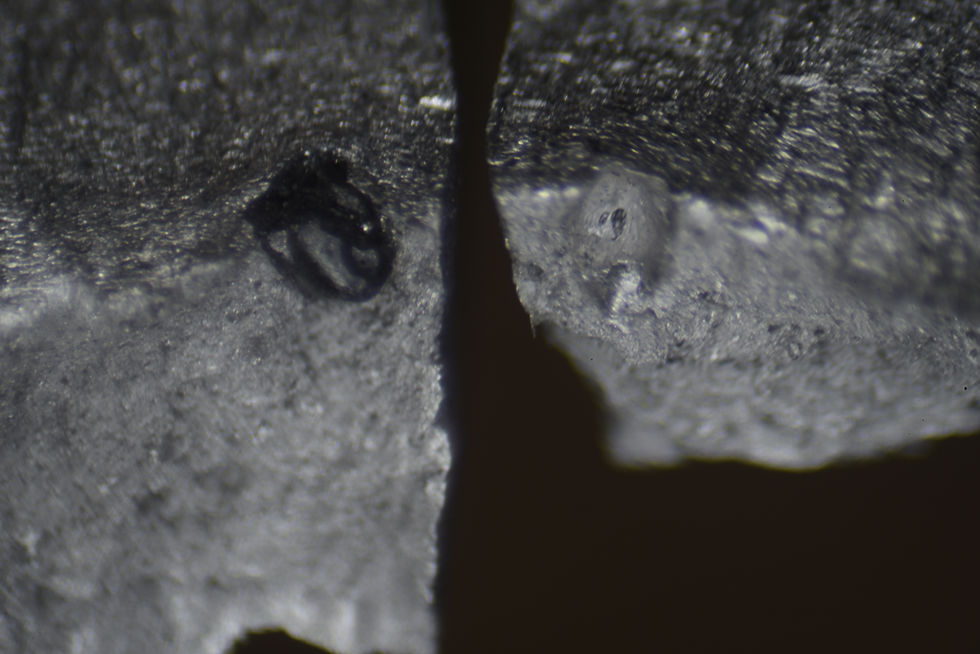
コメント