Router Hold-down Mechanism for Metalcraft Inc.
- Christopher Bettencourt
- Dec 11, 2020
- 2 min read
Updated: Nov 13, 2023
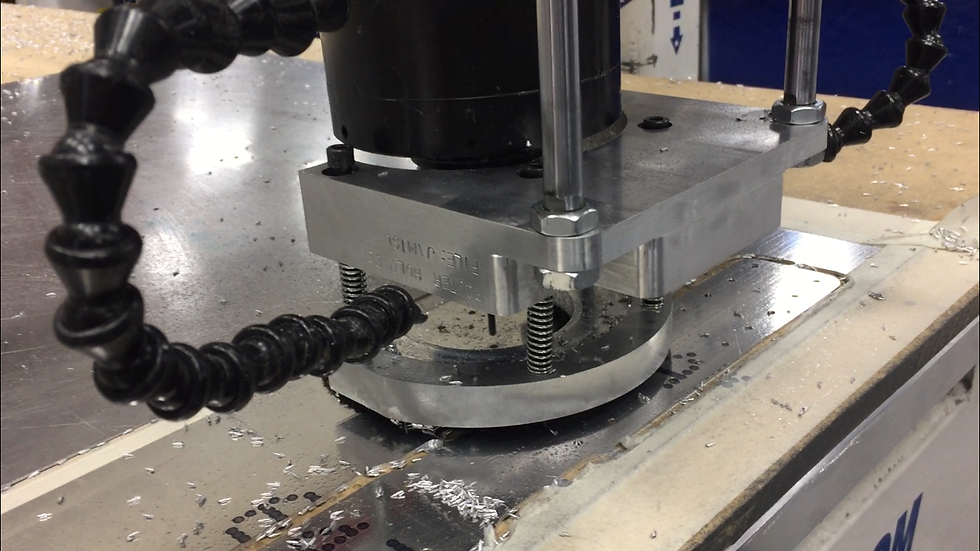
My Project Manager came to me with a problem at the CNC Router. The vacuum wasn't powerful enough to hold down the parts that were being cut out of the blank sheets. Their current solution was to have the operator use a broom handle to hold down the material when the drill bit cut out a part. This caused chip burns and potentially other safety hazards. They told me they had tried several different ideas that ended in failure.
Challenges
This seemed straight forward to solve. I would have something that would follow the drill bit and hold down the sheet metal parts. I discovered some constraints:
The drill bits all had different sizes so the mechanism would have to be adjustable.
The mechanism had to move out of the way during a drill bit change.
Various constraints on dimensions due to equipment and movements.
Misters for coolant need to have easy access to the drill bit.
The sheet metal could not be scratched.
My initial design sketch is shown below with some ideas on how to overcome the challenges. Spring tensioned bolts would give an estimated force of 30 lbs. when fully compressed with the shortest drill bit size. A hinge in the back would allow the base to be pushed out of the way when the drill bit changes. Finally, stiff bristles would allow for the force to be distributed over the surface of the sheet metal without marring the surface.

I designed the prototype in Siemens NX6 and 3D Printed the parts using a Fusion3 3D printer. I calculated the amount of force needed to restore the mechanism back to the normal operating position and implemented a torsion spring for the pin hinge.

This design failed to move out of the way of the moving parts during tool changes, but did prove effective for holding down the sheet metal.
To overcome this issue, Another revision aimed to utilize the Router's built in pistons to slide the mechanism upward and over the tool head to allow for tool changes without interfering with the moving parts.

This material failed to have the required stiffness to keep the mechanism from bending under loads and it was decided to machine the parts out of aluminum.
The final result is shown below.
Comments